Mars Rover Manipal
A Mars Rover robotics team at Manipal Institute of Technology, Manipal
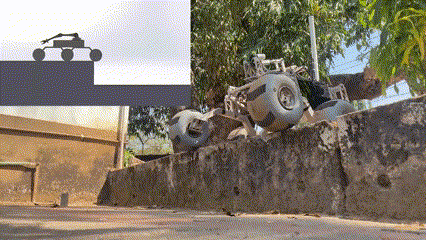
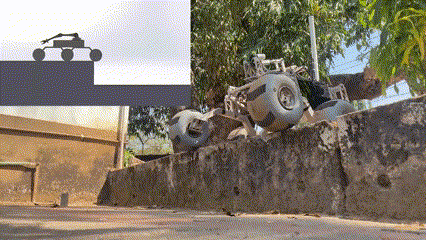
Mars Rover Manipal, is a student robotics team from Manipal Institute of Technology that designs and builds Mars Rovers. The team takes part each year in major competitions, including the University Rover Challenge organized by the Mars Society, the European Rover Challenge hosted by the European Space Foundation, as well as the International Rover Challenge and the International Rover Design Challenge, both led by the Space Robotics Society.
The team designs, manufactures and tests Mars rovers consisting of suspension systems to traverse rough terrain, a 6-Degree of freedom Robotic manipulator, autonomous systems such as LiDAR and RealSense, and a scientific analysis module to analyze soil and rocks.
I was a part of the Mechanical design and Manufacturing subsystem in my sophomore yeah, and went on to become the Technical Lead of the team. As the Technical lead, my main role was to direct the rover's design and implementation, while coordinating the Mechanical, Electronics, AI and Science Subsystems.
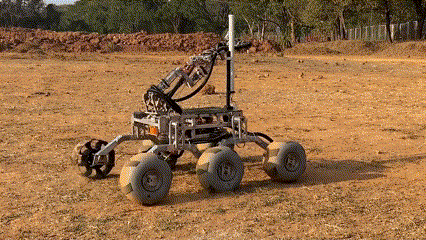
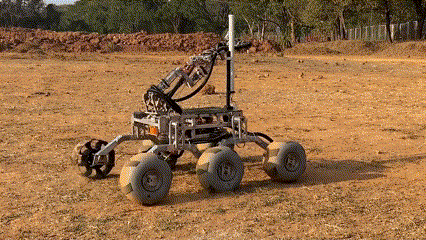
Mars Rover 2021 decending a step (testing & Simulation)
Mars Rover 2021 demonstration video
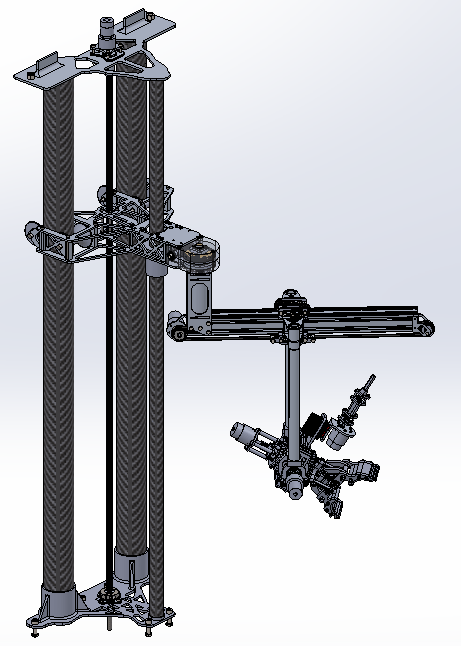
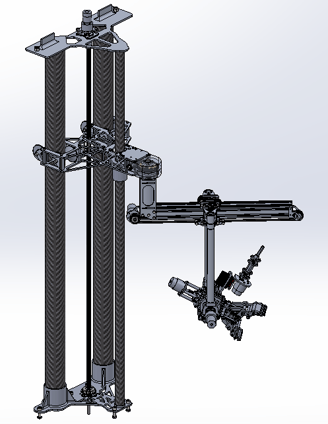
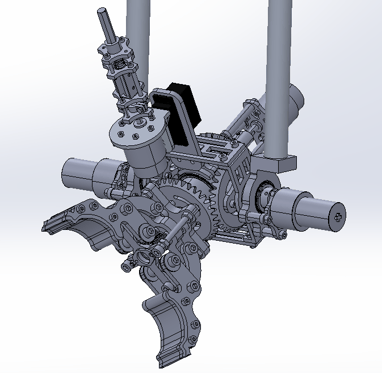

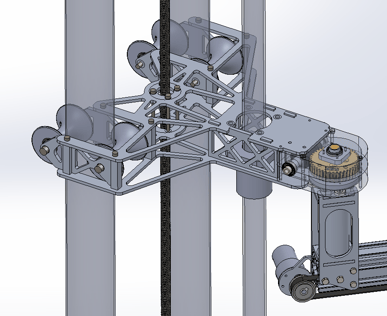

The primary design that I was responsible for was the 6-Degree of Freedom Cylindrical Robotic Manipulator. It was designed using composite structures and analysis, DFM, GD&T, sheet metal design and cost-constrained design, and had the following specifications:
Payload- 5kg
Vertical Reach- 1.2m
Weight -12kg
Lead screw, Worm drive and Timing belt driven 3-DoF's of the Robotic Arm
Bevel Differential and 4-bar linkage based 3-DoF's of the End effector
6-DOF Cylindrical Manipulator design
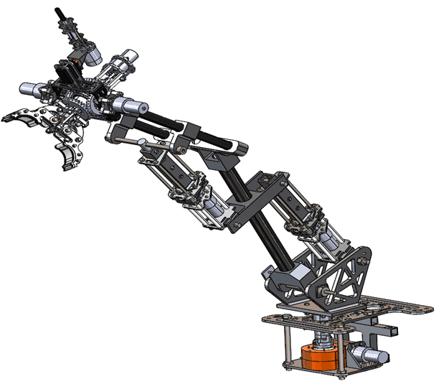
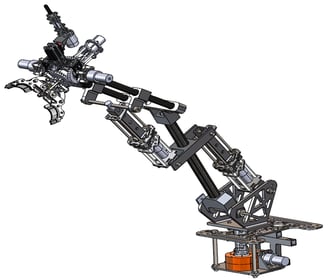
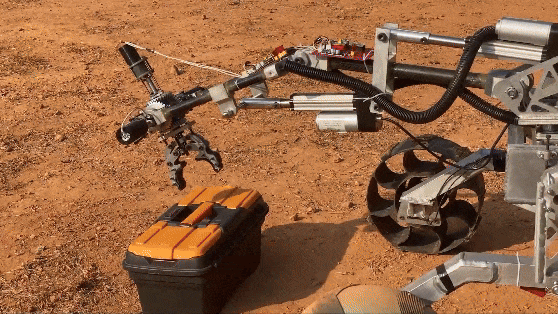
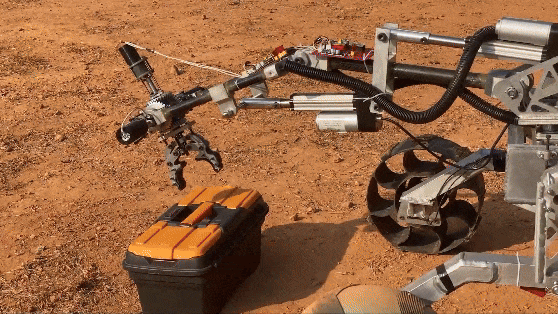
The Worm gearbox and 3-DoF bevel differential end effector were also used to upgrade the last year's competition rover, reducing backlash and improving performance in the pick-and-place tasks. The image of the CAD design depicts the upgraded robotic manipulator, with the image to its right showing the manipulator before the upgrade.
6-DOF Articulated Manipulator
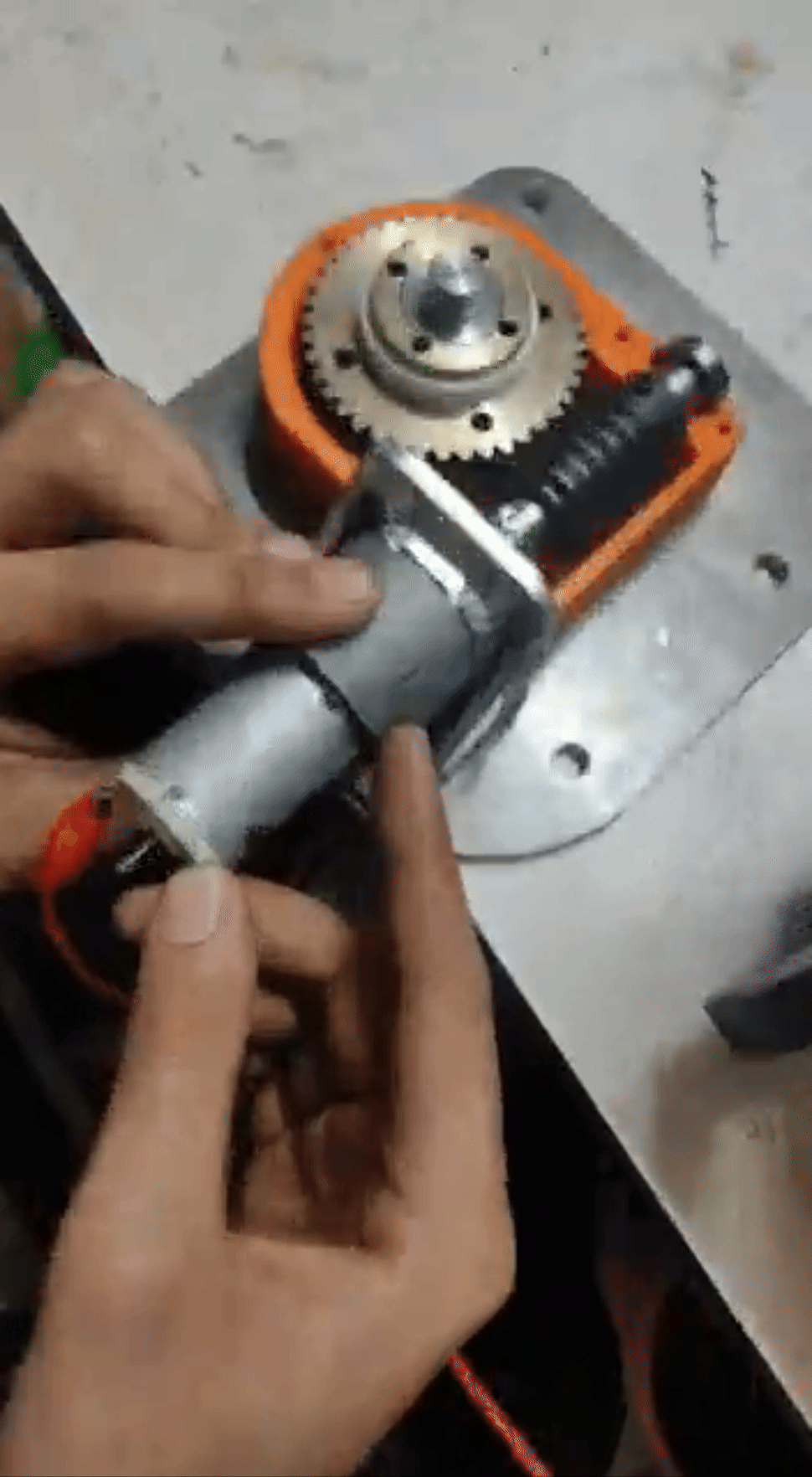
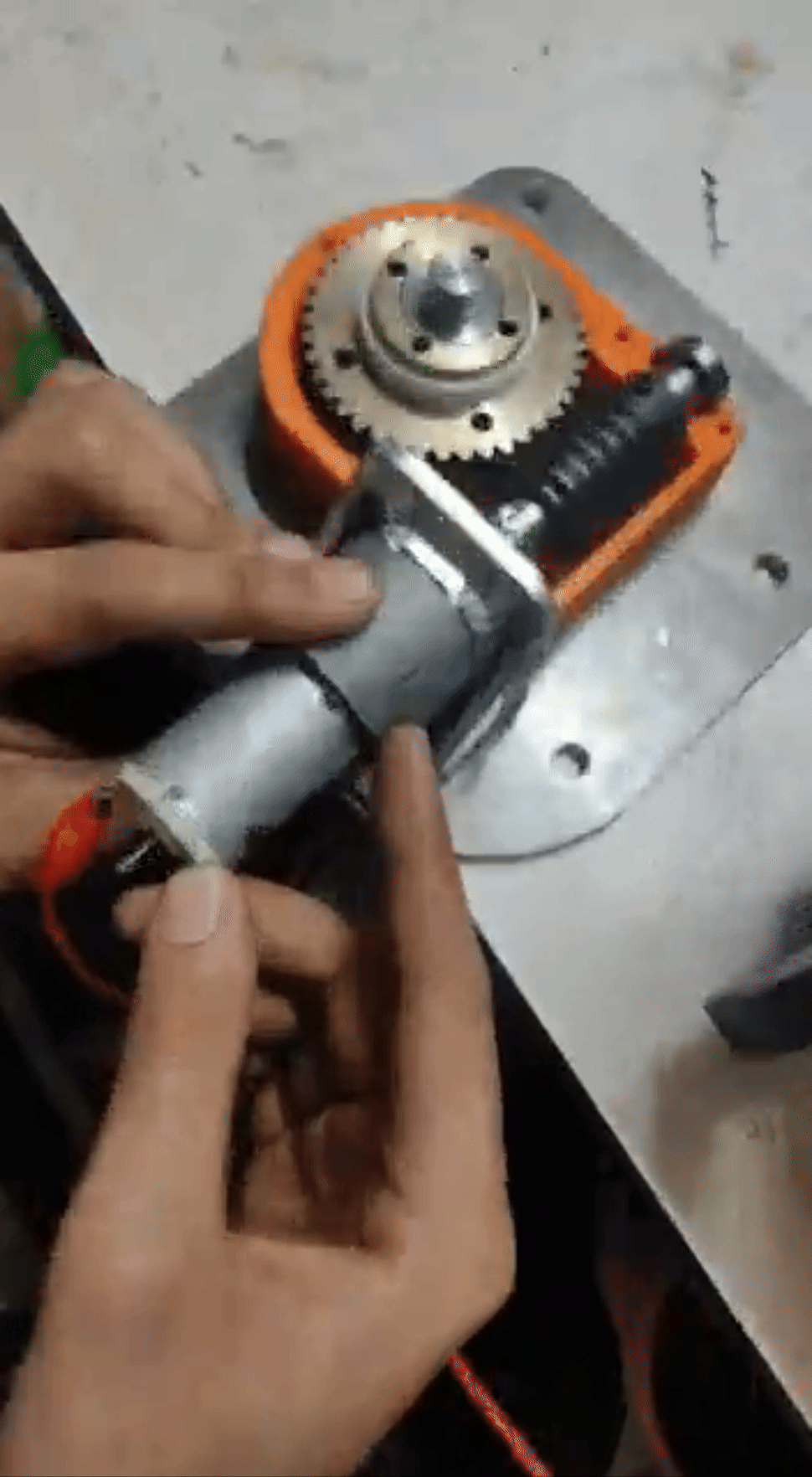
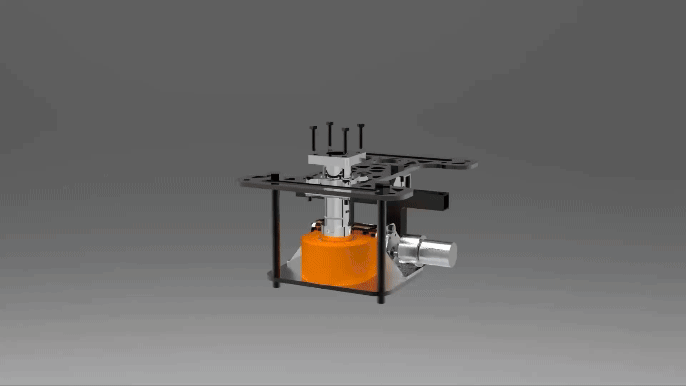
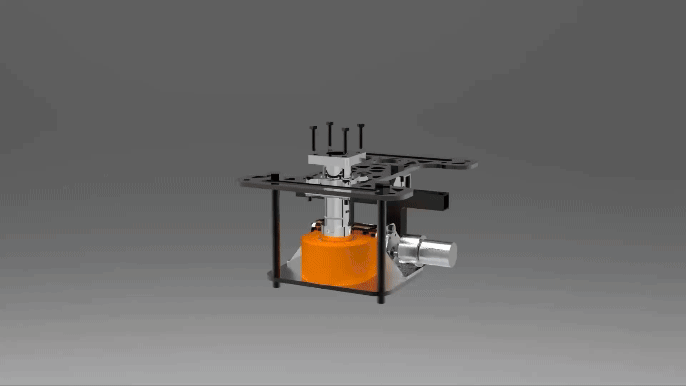
The Worm gearbox below was a major Fused Deposition Modelling (FDM) 3D printing development, withstanding 1800N of peak force for over 18 months of operation. A conventionally manufactured gearbox would be heavier and costlier, hence the FDM alternative was extremely advantageous.
The required structural integrity was achieved by tuning 3D printing slicer (Cura / Simplify3D) settings, while calibrating the 3D printer for dimensional accuracy.
3D Printed Worm Gearbox Assembly
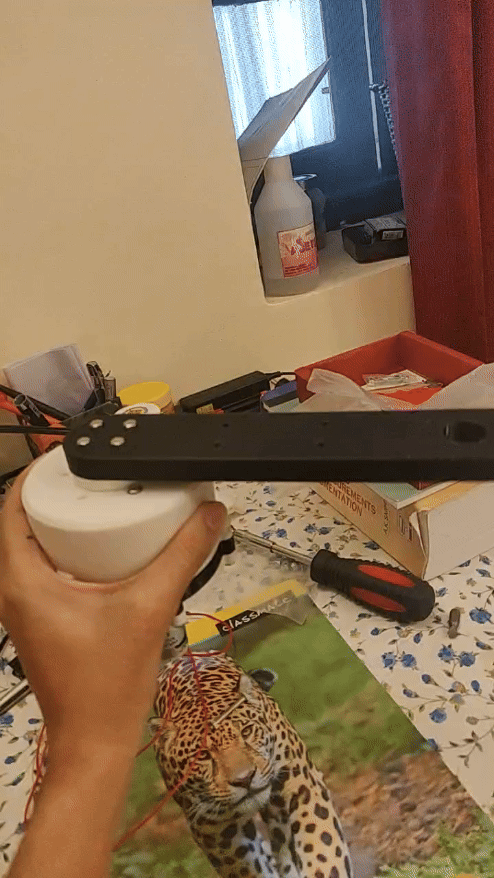
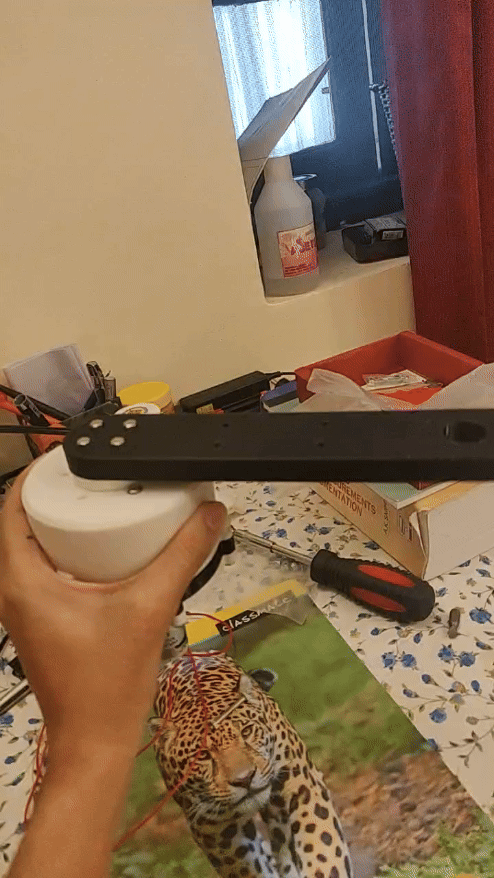
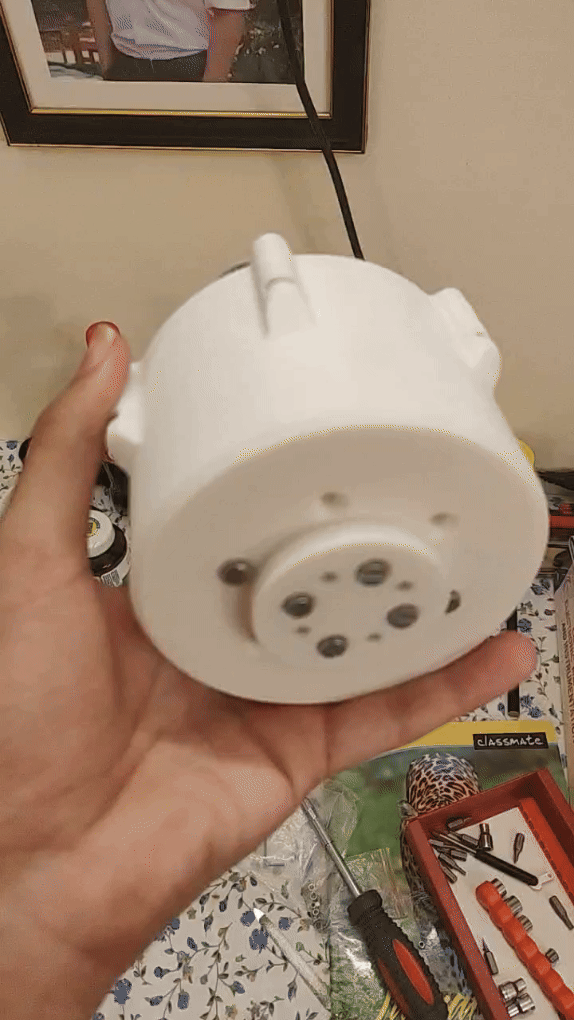
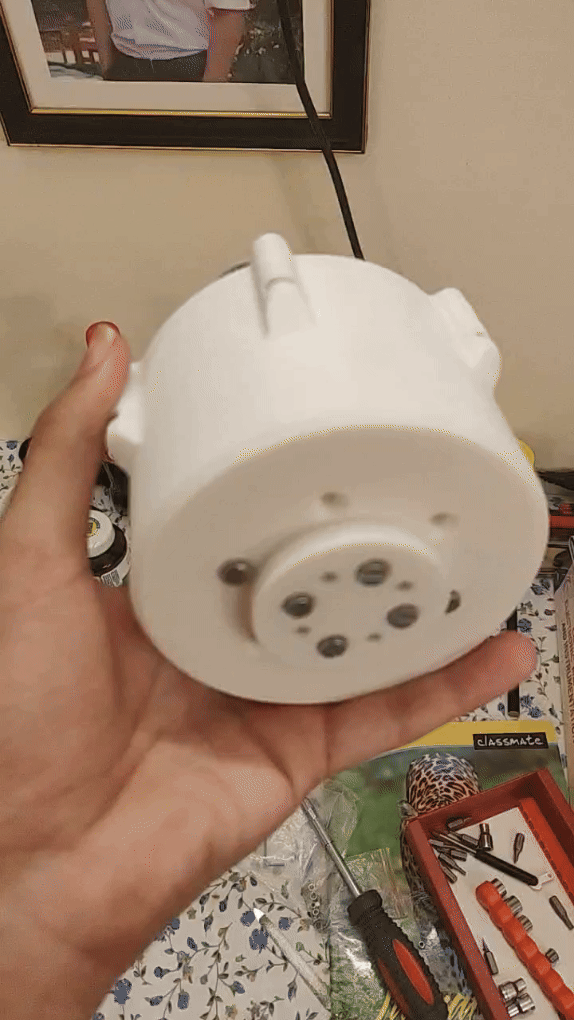
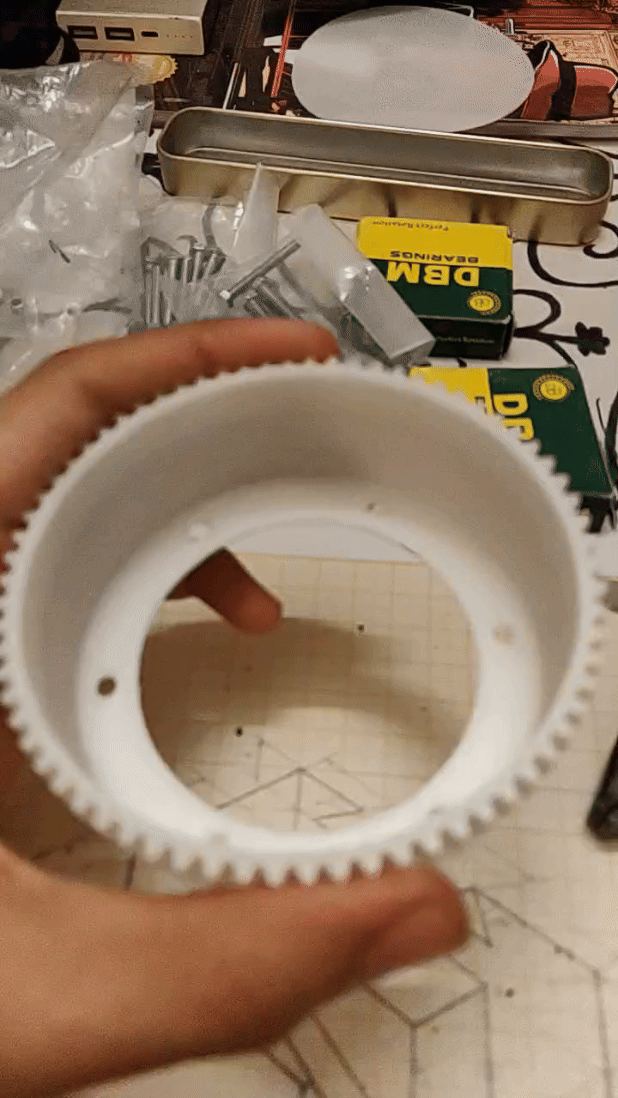
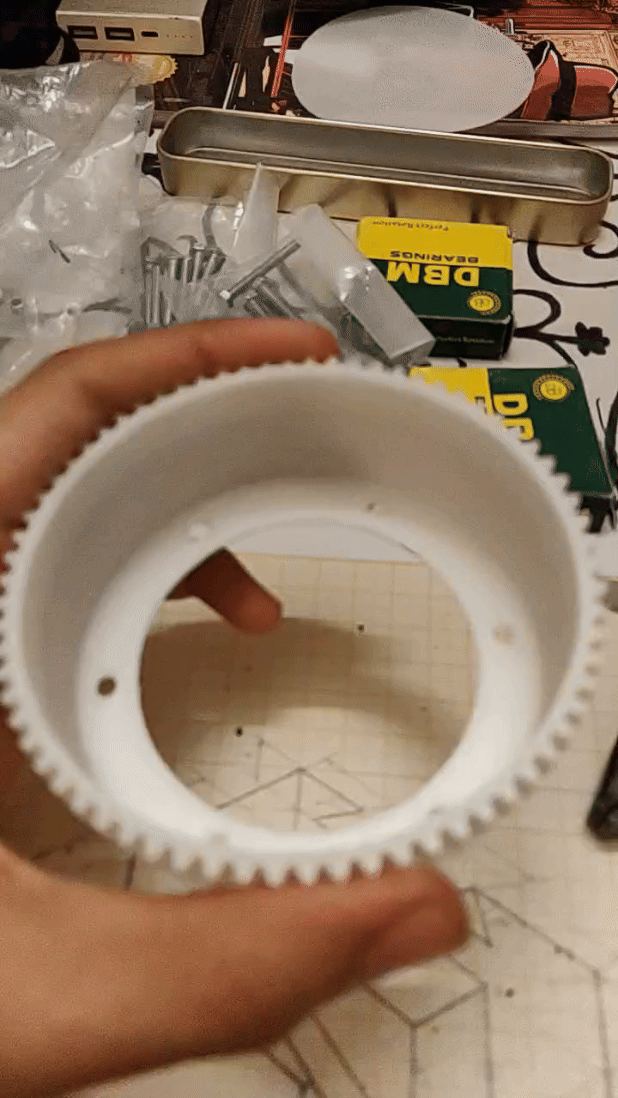
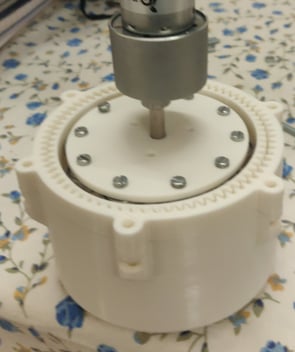
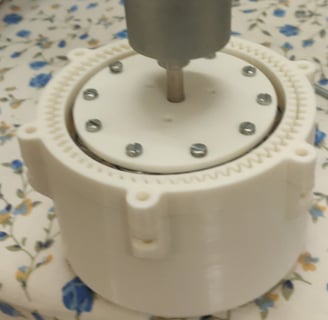
Similarly, a Strain wave gearbox prototype was developed as an alternative to the Worm gearbox implemented in the 6-DoF robotic Manipulator and was fully FDM 3D printed as well. It consisted of a wave generator with 10 bearing contact points, and a parametrically designed tooth profile.
The major challenge that I overcame after tuning 3D printing slicer parameters was the delamination of layers in the flex spline of the gearbox. The gearbox lasted over 10,000 cycles of operation.
3D Printed Strain wave Gearbox Assembly
3D Printed Cup Spline demonstration
Load testing arm for the Strain Wave gearbox
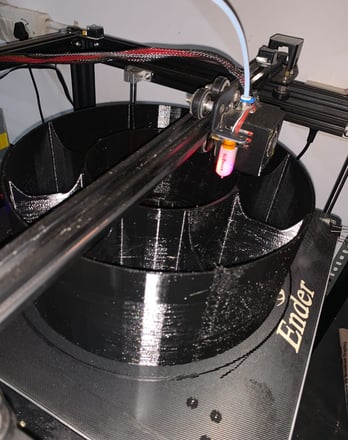

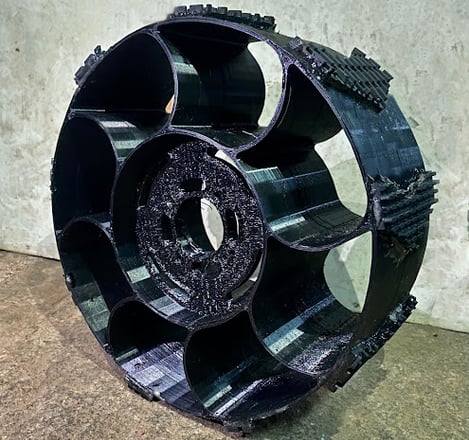
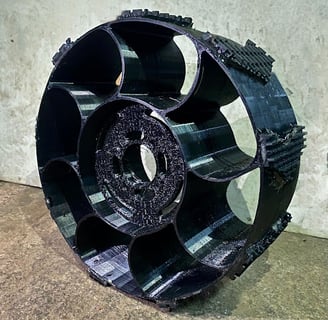
As a research project, I led an effort to develop fully FDM 3D-printed rover wheels that were compliant yet robust. I developed custom 3D printing software (Simplify3D) slicer configurations to achieve the required mechanical characteristics from FDM-printed parts.
I tuned parameters such as Shell count, Shell thickness, Infill overlap percentage, Infill percentage, Wall ordering, Z-seam alignment, Print speed, Travel speed, Print acceleration, and Retraction, all carefully tuned for the best strength-to-weight ratio at the shortest printing time.
3D Printed wheel prototype in PETG with rubber treads
Printing of PETG 3D printed wheel
(Optimized time to print: 30 hours)


The Scientific Analysis module comprised of augers, collection trays and an analysis area which contained petri dishes. Chemical solutions and agents were added to soil and rock samples using peristaltic pumps, and the results were studied via camera observation and UV spectrometers.
During my tenure as the Technical Lead of the team, I was the interim Science subsystem lead as well, managing operations and tasks. Under my leadership and technical design guidance, the Science subsystem won the "Best Science Team" award at the University Rover Challenge (URC) 2022.
My contributions were to the indexing mechanism of the multi-auger tray, the auger's geometry to ensure optimal sample collection and implementation of the peristaltic pump systems.
Scientific Analysis Module (Multi-Augur system)
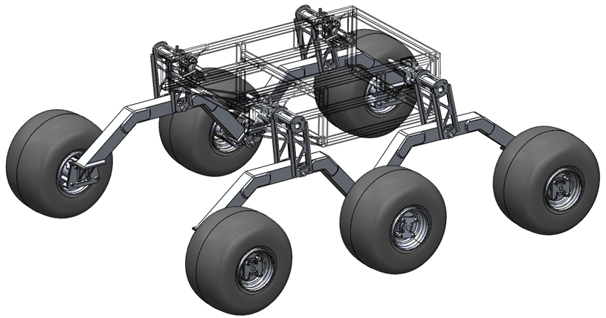
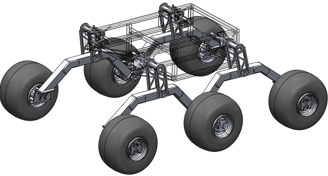
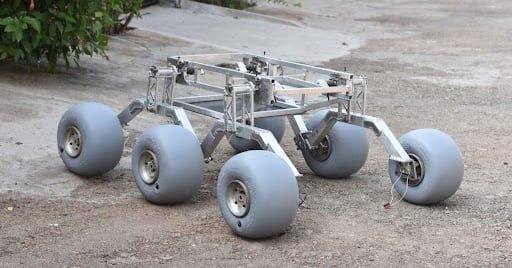
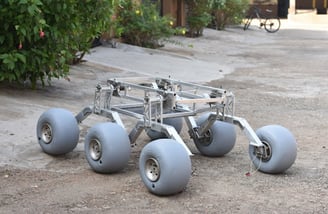
Following is the novel 5-bar mechanism rover suspension developed, constrained by torsion springs, and manufactured with TIG welded aluminum sections.
5-bar Multilink Suspension
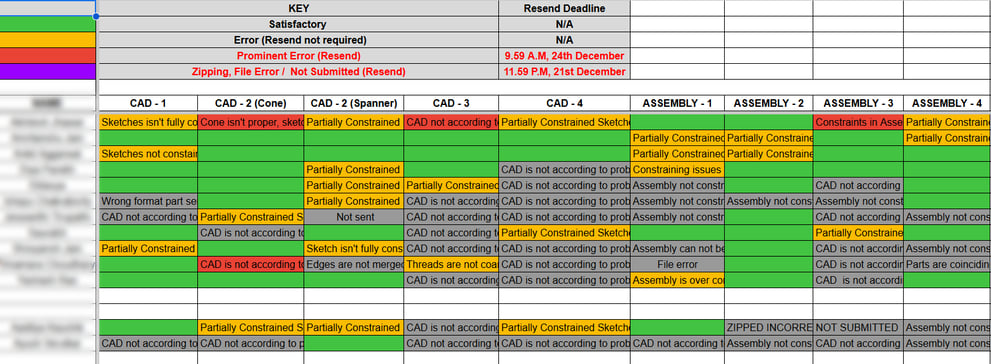
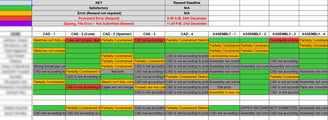
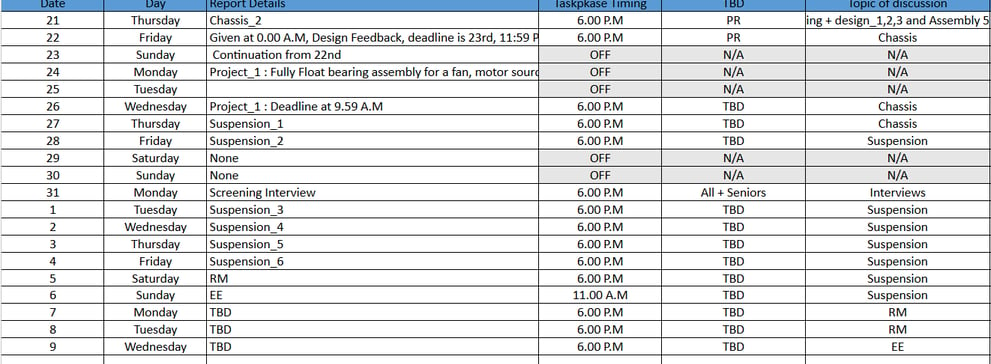
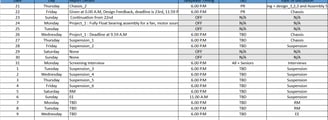
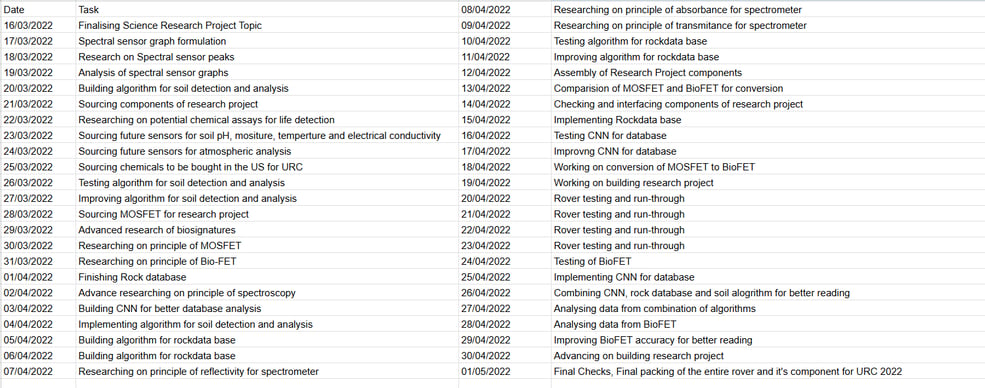
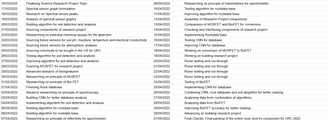
As the Technical Lead of the team, I organized and planned the training, recruitment, and manpower utilization of the team. Following is an example of the "Design review" session task sheet for the training of recruits in the team.
Following is the month-wise training plan for the new recruits on the team's Mechanical Design and Manufacturing Subsystem.
As the Interim Science Subsystem Lead in 2022, I planned discussions and reviews with the team members, ensuring timely work and fund management.
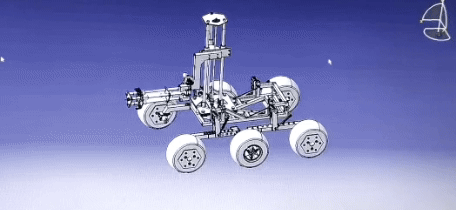
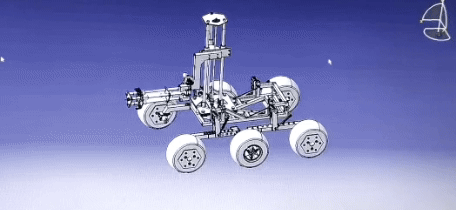
During the 10-month training period in the Mechanical Design and Manufacturing Subsystem, the following Rover was designed by the recruit's batch. This was a 1-month task completed in the winter of 2020.
I was tasked with the design of the 6-DoF Cylindrical Manipulator and performed FEA analysis, motor and joint torque calculations, lead screw loading calculations, and bearing assembly design.
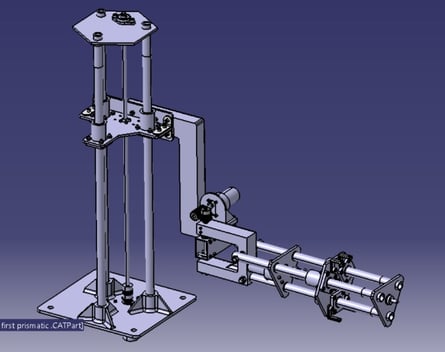
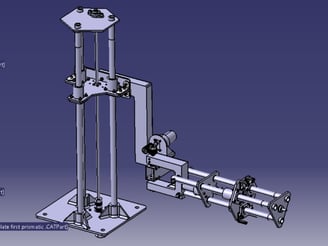
In the initial stages of training, each of us was tasked to build up our own Mars Rover CAD, independently designing each module such as the chassis, Rocker-Boggie suspension system with a bevel differential, drive and transmission assembly, and robotic manipulator with a 4-bar mechanism-based gripper.
The design iterations, FEA simulations, and mechanism design were all performed from scratch as a learning activity.