Unmanned Ground Vehicle
At ARTPARK, IISc Bangalore
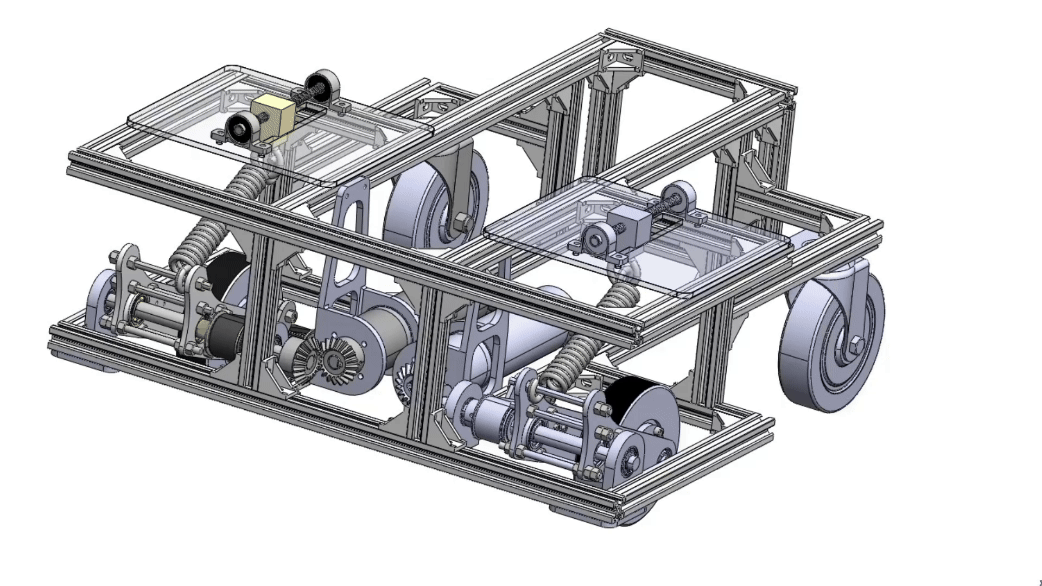
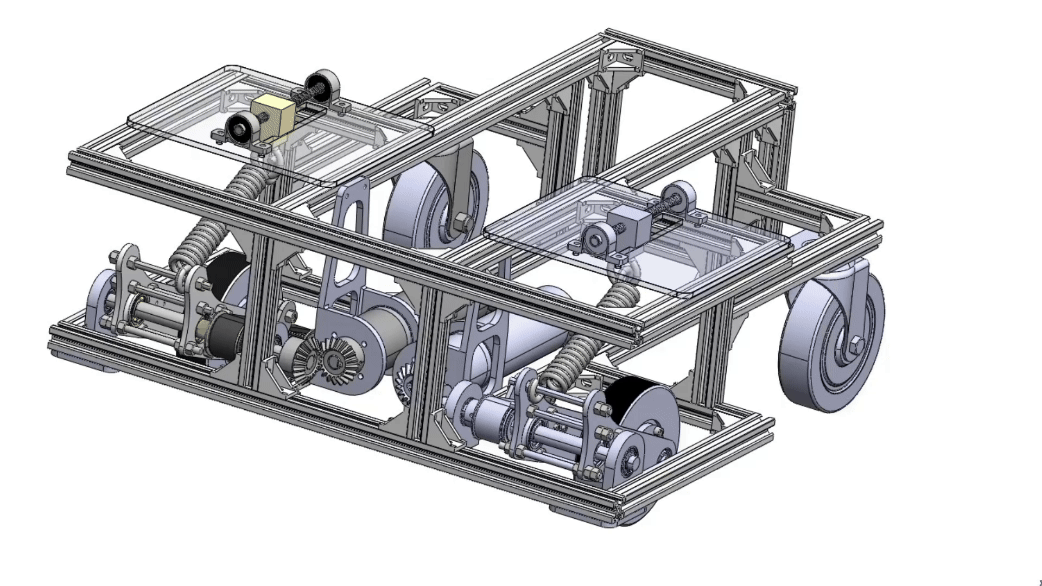
During the summer of my junior year at Manipal Institute of Technology, I interned at the A.I. Robotics and Technology Park (ARTPARK), a robotics incubator at the Indian Institute of Science (IISc), Bangalore, under the supervision of Dr. Kaushik Sampath. I was tasked to build an Unmanned Ground Vehicle (UGV), as a mobile base for a hospital robot. The UGV was to be designed to have a payload of 40kgs
The robot was supposed to conform to building and hospital codes for safe traversal inside the hospitals, and this determined the maximum width, maximum slope angles, and general payload requirements. The proposed robot had a swing arm suspension system, which helped the robot maintain ground contact.
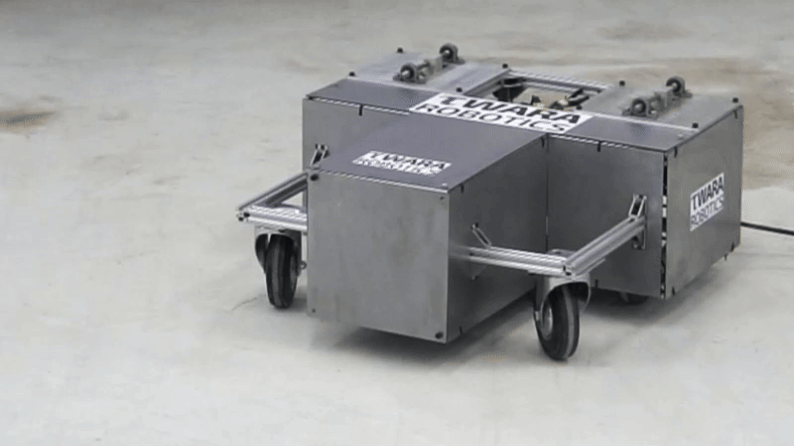
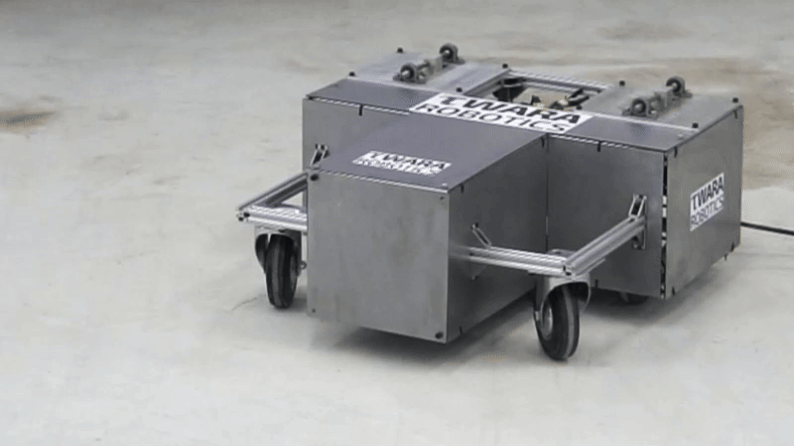
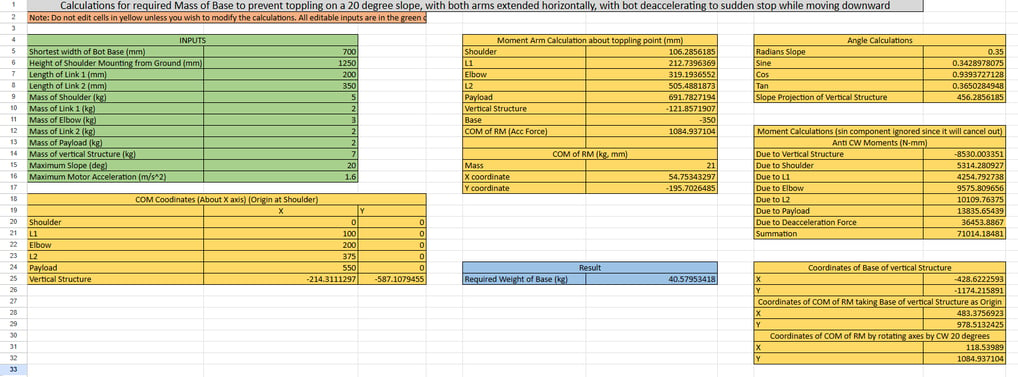
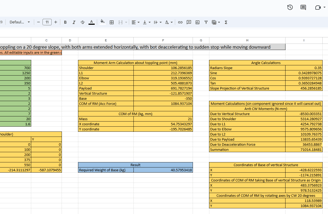
Since the payload on the UGV (consisting of a tall frame and a robotic arm) would result in a high center of gravity, Stability calculations were done to ensure that the robot's stability polygon is sufficient to manage the payload without toppling. Parameters such as the Center of Mass (COM) of each section of the robot, maximum slope angle, maximum acceleration, track width, and wheelbase of the robot were considered in the calculations.
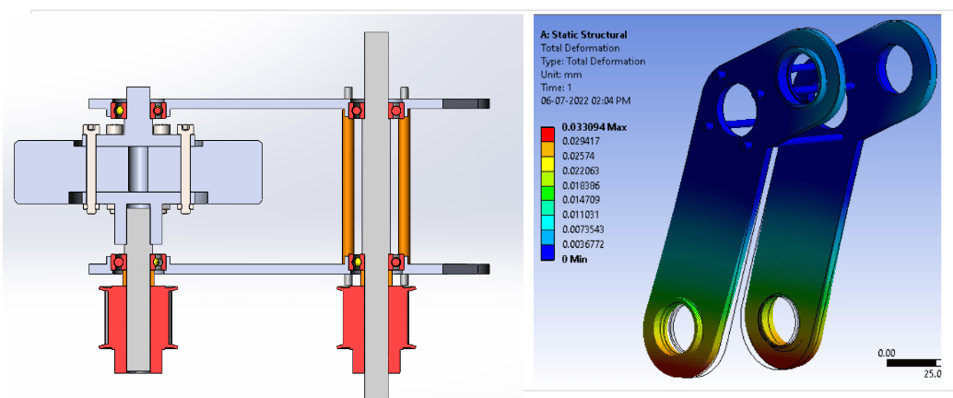
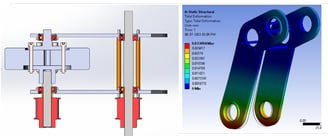
The suspension bearing assembly was designed to transmit power to the drive wheel through a belt drive and miter gear assembly. The suspension links and mounts were simulated using Finite Element Analysis software to optimize the weight of the parts.
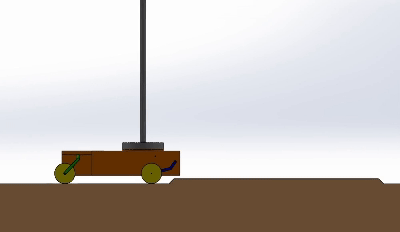
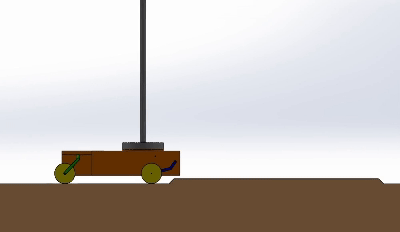
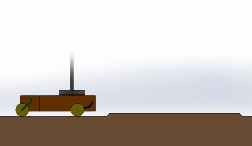
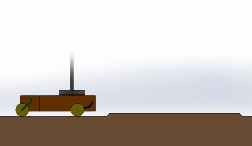
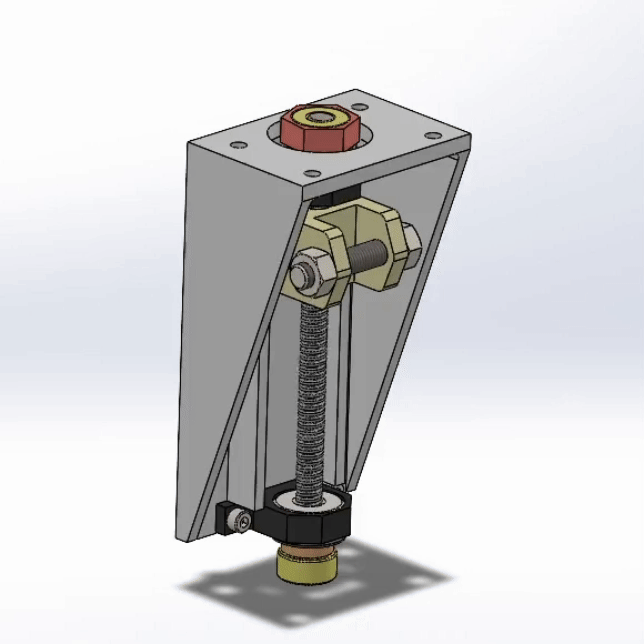
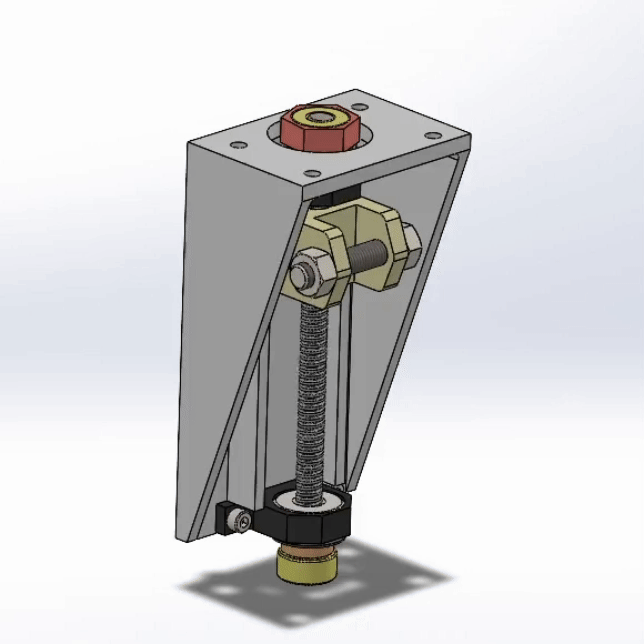
The suspension system, constrained by extension springs was simulated in SOLIDWORKS motion, to ensure the suspension geometry traverses standard obstacles according to Hospital codes (Steps, railing, etc.). The simulation videos below compare the UGV without suspension (LEFT) to those with suspension (RIGHT). A screw-based pre-load assembly was implemented to adjust the extension spring pre-load based on the payload on the UGV.
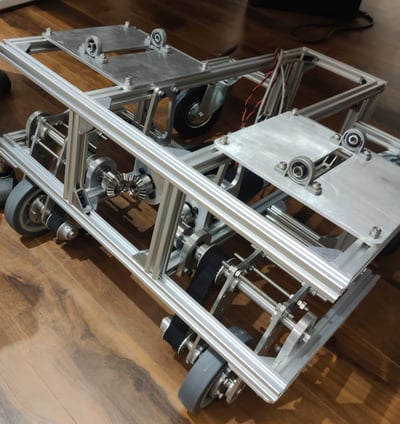
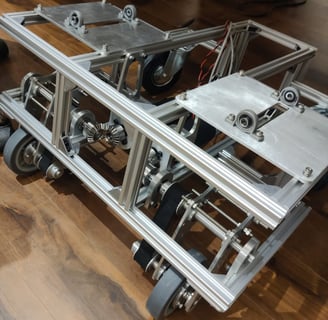
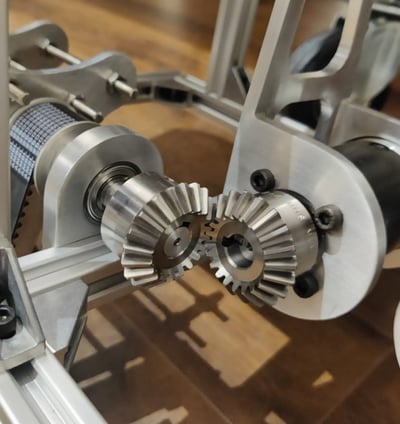
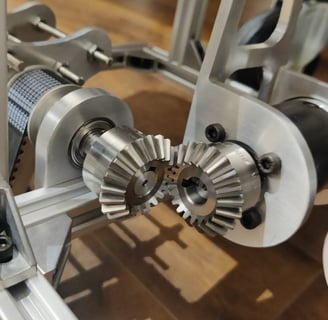
Following is the manufactured and assembled UGV, showcasing the belt drive, miter gear assembly ad pre-load assembly.
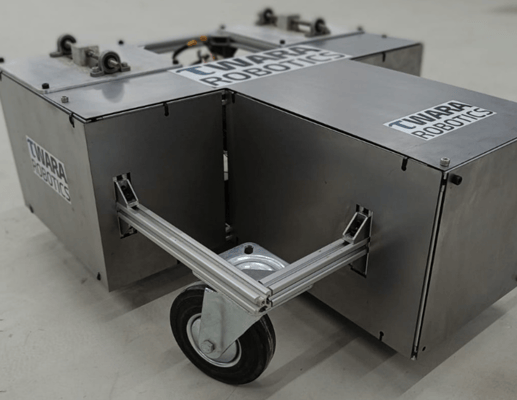
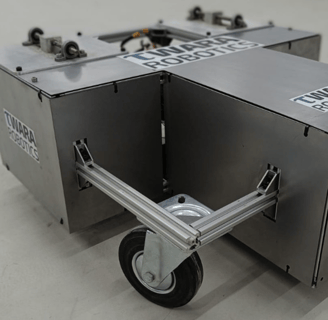
In 2023, the UGV was repurposed as a testing platform for ongoing research and development, and body panels were added to complete the UGV. Two different sheet metal-based bodyworks were designed. The enclosures were used to make the UGV collision-safe among human operations and protect it from external contaminants.