Remote Controlled Aircraft - Aeromodelling
Through 2017-2021
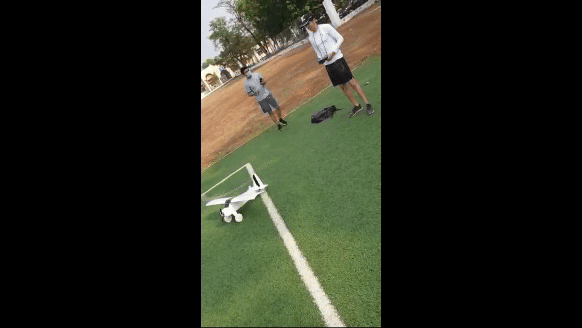
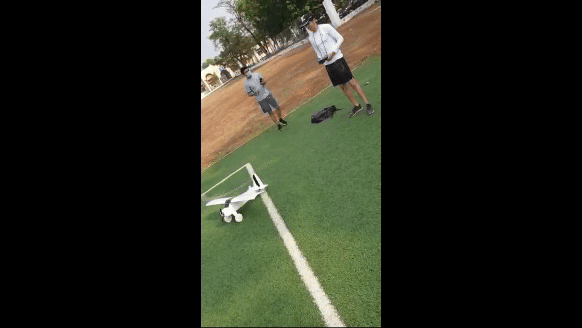
Throughout my high school and Undergraduate studies, I have been an avid designer, builder, and pilot of remote-controlled (RC) aircraft. Over 5 years, I have built 20 RC aircraft using a mix of EPP foam and 3D printed parts. An archive of the major designs I made throughout the years is below.
Starting with the latest aircraft, a bush plane dubbed "RC Cub", was an EPP foam aircraft. It had a 45’’ wingspan and used a 1400kV BLDC motor paired with a 10x4.5 propeller, run by a 30A brushless ESC with Simon-k firmware, four 9g servos and a 6-channel R/C transmitter and receiver.
Bush Plane - RC Cub
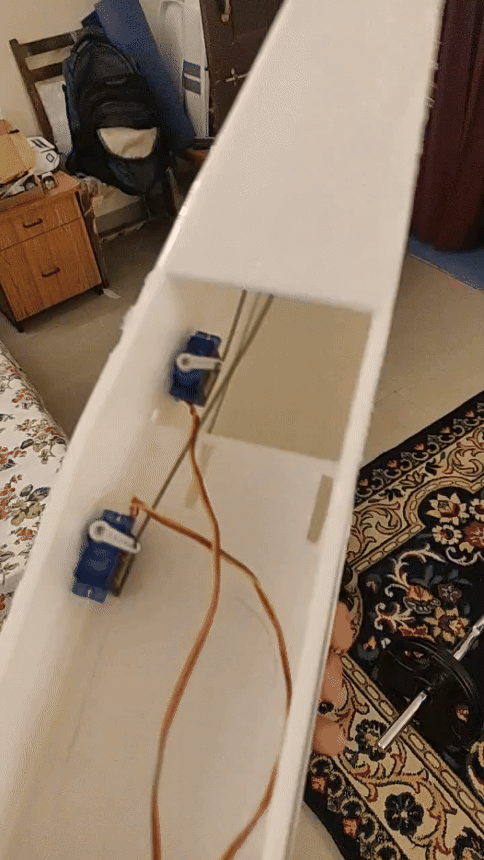
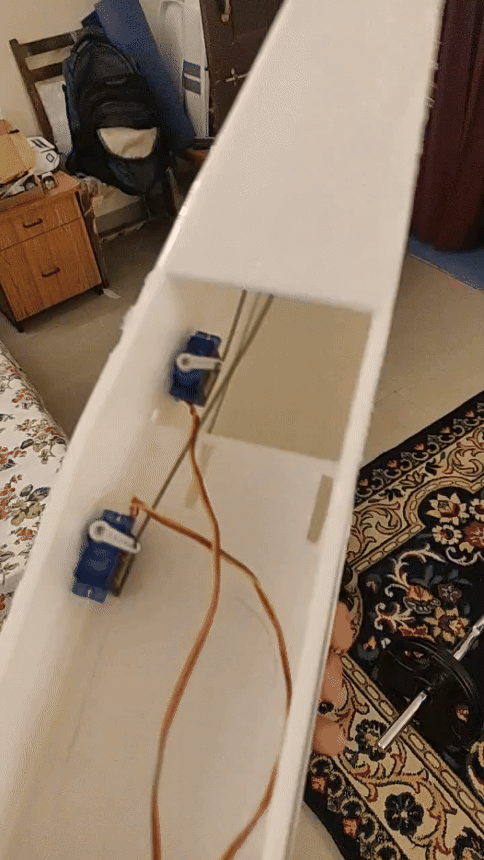
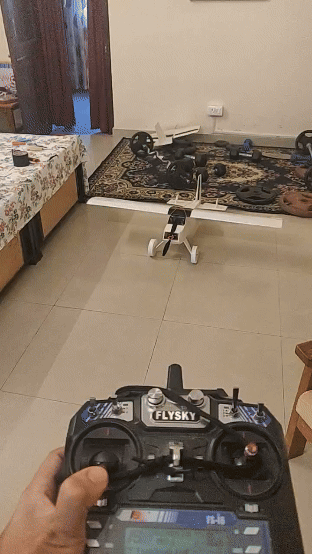
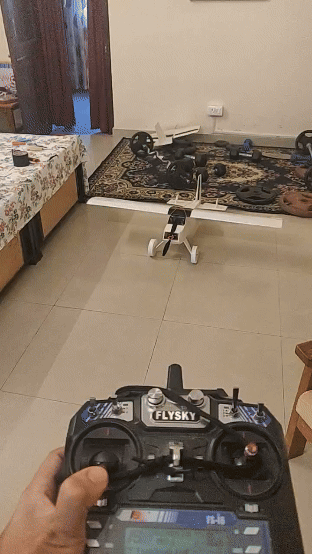
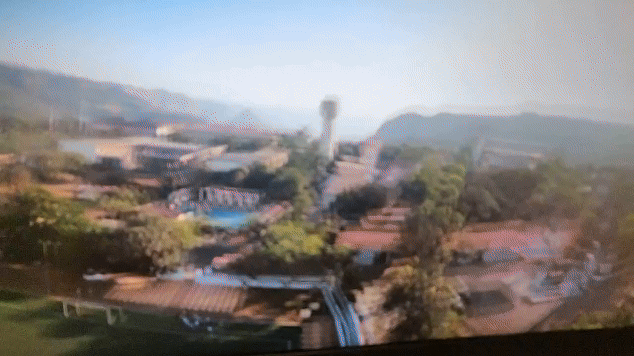
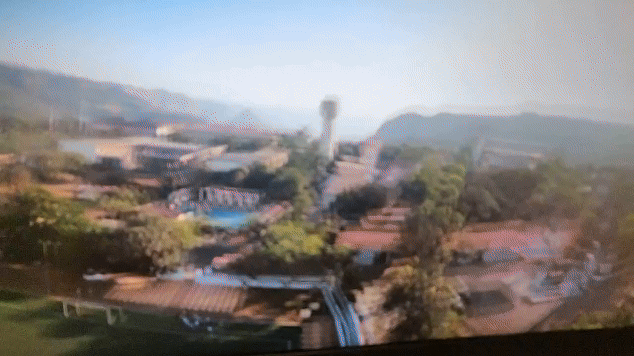
RC Cub take-off footage
Fuselage and Tail section build
Completed RC Cub and pre-flight checks
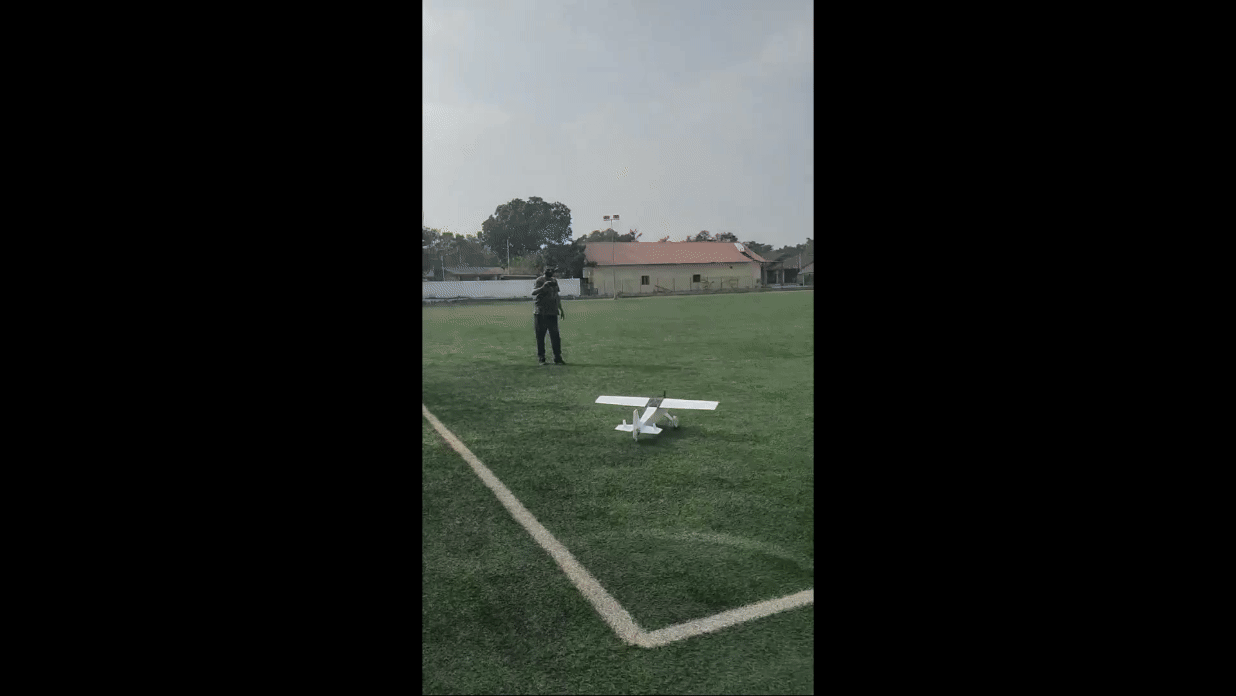
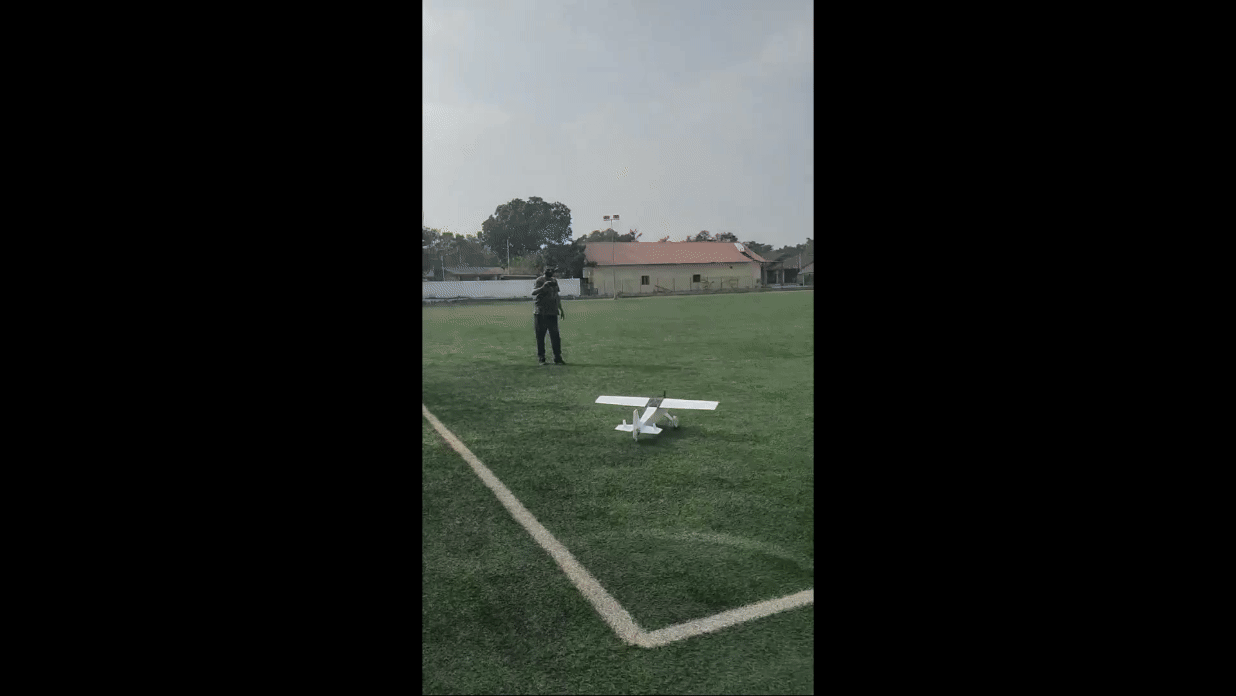
On-board flight footage from the
RC Cub
Having procured an FDM 3D printer during the COVID-19 lockdown, I wanted to experiment with a fully 3D-printed aircraft, with the fuselage, wings, and control surfaces, all 3D printed out of PLA filament. The 3D printing slicer software was tuned to ensure a high strength-to-weight ratio.
3D printed (Fused Deposition Modelling) RC Aircraft
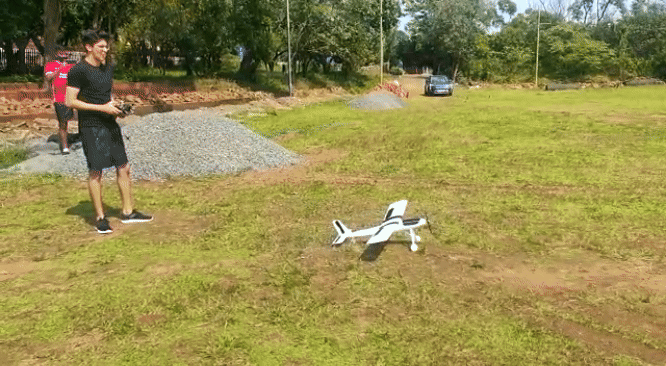
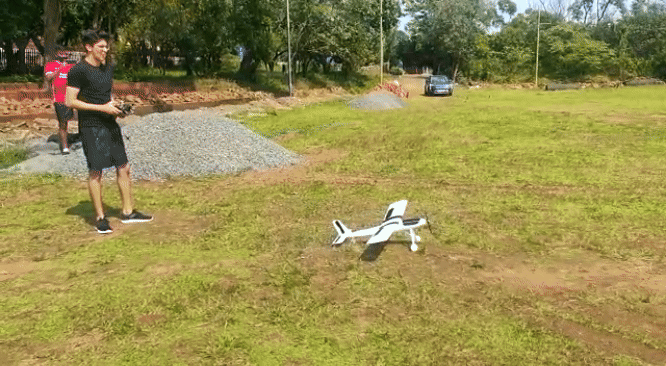
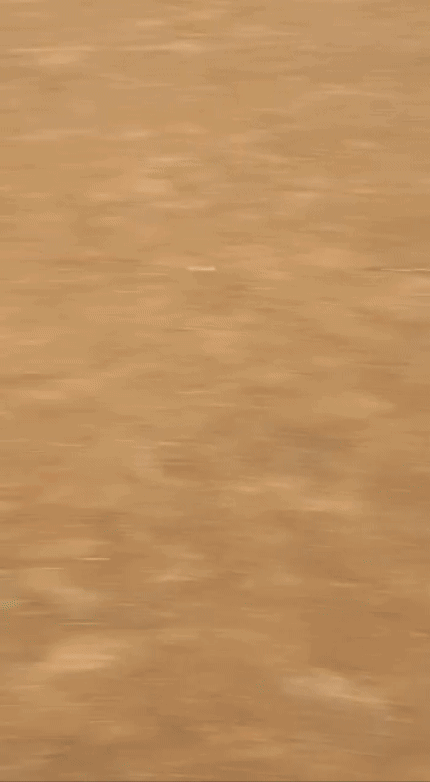
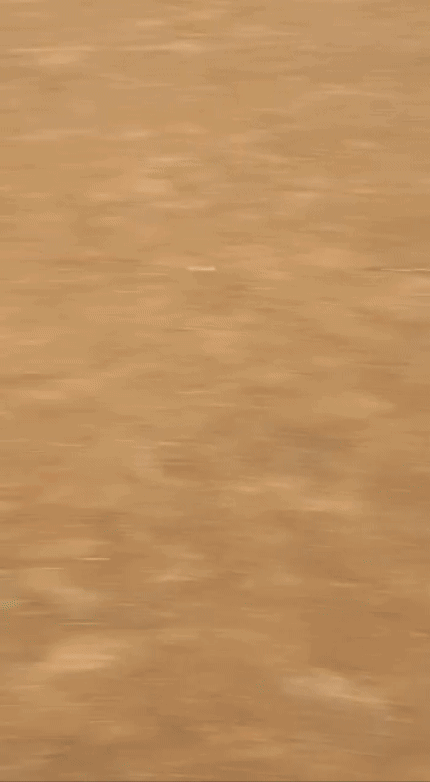
3D printed RC aircraft test flights
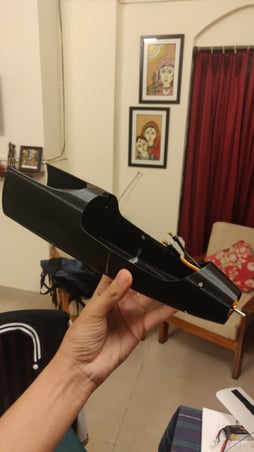
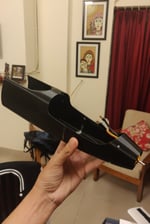
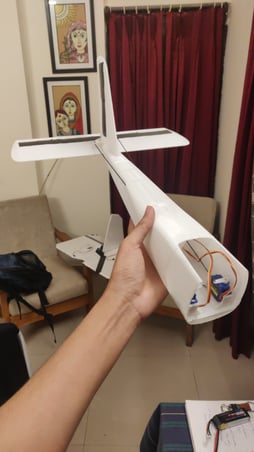
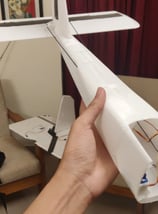
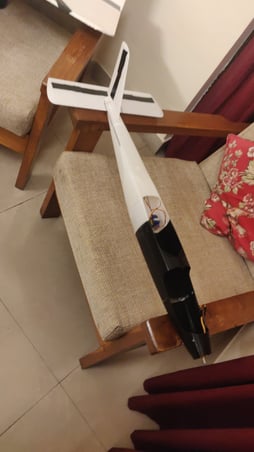
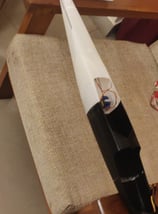
Nose section 3D printed and assembled
tail section 3D printed and assembled
Fuselage assembly and servo motor installation
First test flight
During TechTatva'19, the technical fest of Manipal Institute of Technology, I participated as a solo contestant in the aeromodelling competition called SkyRush. The design constraints required:
Thrust-to-Weight ratio of 1:1
Payload carry and drop capabilities (For a task)
Fly for 30 minutes on a standard battery capacity provided.
I designed and built an Omni wing Aircraft, which have excellent efficiency due to their low drag, since the tail is absent.
SkyRush 2019
An aeromodelling competition at the Technical Fest of Manipal Institute of Technology
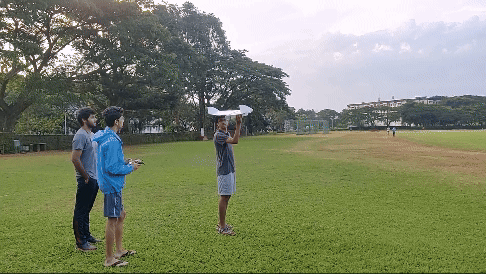
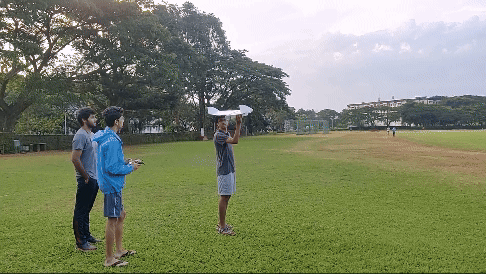
Test Flight of for SkyRush Omni Wing
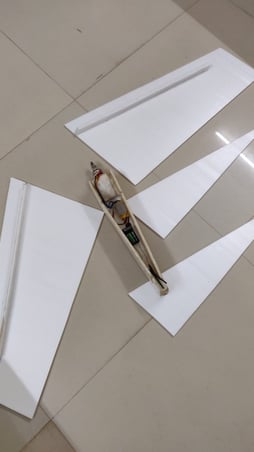
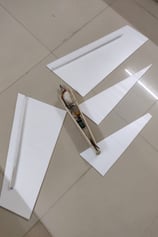
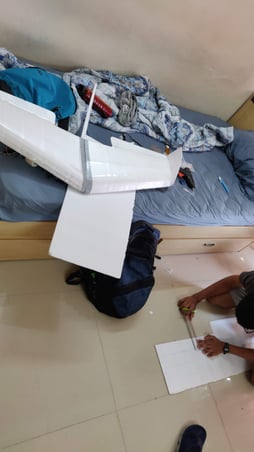
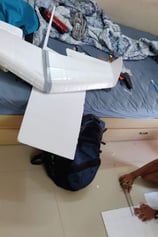
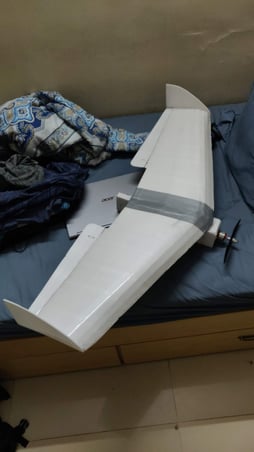
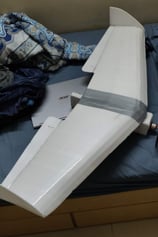
EPP foam build and electronics installation in the fuselage
Build progress of the Omni wing
Completed SkyRush Aircraft
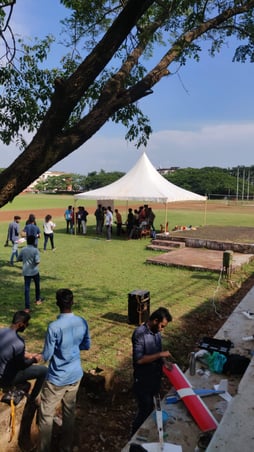
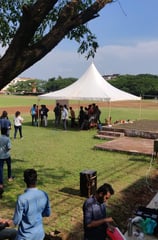
Competition Site - SkyRush 2019
The Aerothon 2021 was based on designing a high-payload combustion engine aircraft, including CFD analysis and CAD design. The Airfoil used here was a Clark-Y airfoil, and a 49cc nitro combustion engine. The fuel tanks were strategically placed w.r.t the payload hatch, to balance the Center of gravity.
SAE Aerothon 2021
A university-level aircraft design competition organized by the Society of Automotive Engineers (SAE)
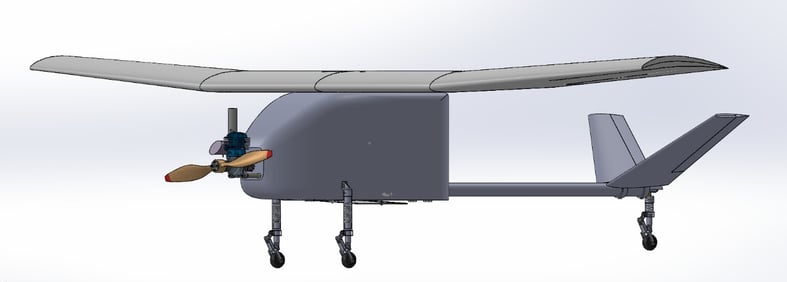
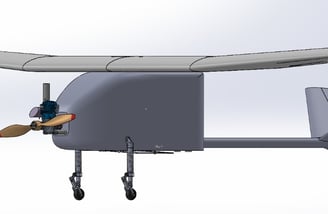
Test Flight of
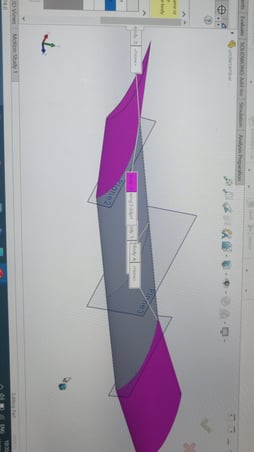
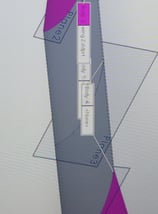
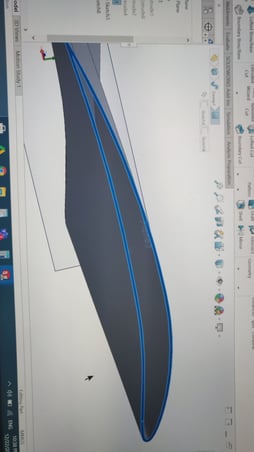
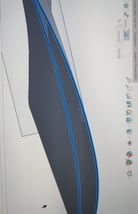
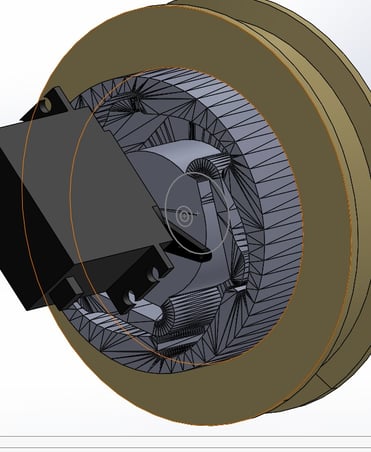
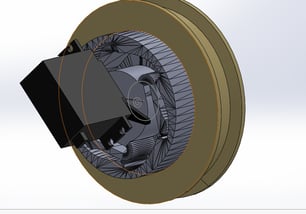
Wing design with polyhedral angle
Clark-Y airfoil for high lift and low drag
Servo-based ratchet mechanism for trapdoor actuation
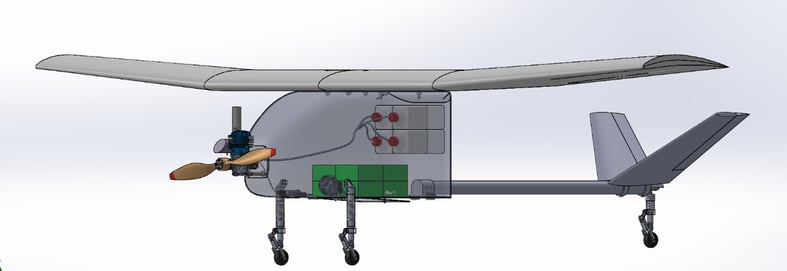
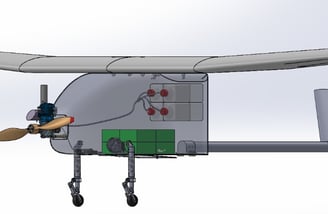
SAE Aerothon 2021 aircraft design, showing a transparent version exposing the fuel tanks, payload, payload mechanism and IC engine.
It has a 72’’ (6 feet) wingspan and is made out of EPP foam, aluminum rods, and fiberglass tape. The electronics used in the aircraft are a 1400kV BLDC motor, spinning a 10x4.5 propeller, run by a 30A brushless ESC with Simon-k firmware, four 9g servos, and a 6-channel R/C transmitter and receiver.
It flies stable with a 2200mAh 3S LiPo battery and has a maximum payload capacity of 900g or approximately 2 lbs. With these specifications, it has a maximum flight time of 35 minutes, the range being 1.5-2km, depending on the flight environment and weather.
Early Designs - Big Cargo Aircraft
A design I built in High School (2018)
Completed RC Cargo Aircraft with a 6 feet wingspan
EPP foam building process
Assembly of fuselage and wing
EPP foam building process